MoreorlessMusic
Member
This post is rather long so I have had to break it up into at least two parts. I suggest putting the kettle on and having a cuppa about half way through if you get that far! I thought it was about time I did a follow up to the post that I did about the damaged and unplayable 80 bass Scandalli accordion that I acquired back in May of 2024. A link to my earlier post about the Scandalli
The job of restoring the Scandalli was an adventure that took a few hours a day for 3 or 4 weeks. I had not done anything like this before, and was very new to playing accordions, having only begun that earlier in the year.
The little 12 bass Scandalli that I made my first accordion noises on, needed new valves, as evidenced by the clatter and flap of curled leather when ever low note were attempted, so my restoration of the 80 bass Scandalli really begun with opening up the 12 bass, taking out its reed blocks, removing the reeds, replacing the valves, and doing my first attempts at re-waxing.
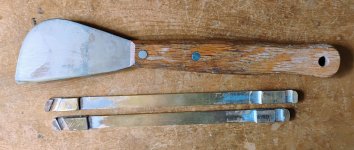
I made my own reed wax from 3 parts of beeswax, 1 part of pine resin and a few drops of linseed oil, and I made my own waxing tool after watching videos of Italian accordion makers waxing reeds with those half moon shaped tools that look rather like a modified cake slice. And yes I did go through the kitchen drawers to see if I could find something there that might work! In the end I flattened and reshaped an old paint scraper that was made out of heavy stainless steel, and had a simple wooden handle. Waxing reeds was terrifying at first, and my initial attempts were like the frenzied splashes of an abstract expressionist painter from the 1960s, but I learned a lot by being brave and giving it a try and I got better at it. I now enjoy the process and look forward to the delightful aroma of warm beeswax and pine resin that I heat up in an old electric crock pot.
With the 12 bass accordion back together again and working, it was time to have a serious look at the 80 bass Scandalli. When I acquired it, the instrument really was unplayable, with some notes not sounding in the treble, or groaning like an animal in pain. All the register switches were jammed, and when I popped the front cover off I could see that many of the pallets were in very poor condition owing to insect damage and, very strangely, what looked like an excess of heat that had distorted some of the pallets.
I realised that I would need to sort out the pallets before I could achieve a great deal, so I did a lot of searching online for replacements that would be suitable. Eventually I found that Wilson Music Services in Canada had a set of Hohner pallets that were in the“Discontinued and Hard to Find” section of their website, nice aluminium ones with red felt pads that were 49 x 13mm and just 1mm greater in length and width than the black plastic palettes on my Scandalli. I ordered them and hoped I could make them fit.

I removed all the treble keys, which was easy to do as each key was held in place by a small metal spring that could be unhooked from its attachment by using a little tool that Scandalli thoughtfully mounted in readiness just above the treble pallets. I attached a numbered sticky label to each of the keys and laid them out in order as I removed them so that I would have less difficulty sorting out the puzzle when I put them back together again. I gave all of the keys a good clean, and also got into all the nooks and crannies behind them with the vacuum cleaner and got rid of 60 years worth of dust! On close inspection of the keys I found some of them had fine metal fragments imbedded in them. I wondered if the instrument had been left open on a bench in a workshop near where someone was grinding metal or welding?
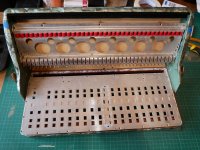
With treble keys removed, I took the opportunity to investigate the treble register selectors. It transpired that these were not working because the register slides had all jammed due to corroding and forming almost commercially exploitable quantities of aluminium oxide! The slides occupy a space between two sheets of metal like bacon sandwiched in between two slices of bread. Annoyingly I could find no way of separating the metal plates, but eventually got the register slides moving by inserting a small screwdriver into the narrow gap between the plates and gently levering away at this until I could get the slides to budge a tiny bit at a time. I hated having to use a screw driver in this manner, but it worked and eventually I was able to remove the slides and carefully clean them, before putting them in their slots again. It was a considerable relief to get them going again.
I removed the old pallets by carefully heating the metal arm that they were attached to with a soldering iron. All of them dropped off easily, and I was delighted to find that the rubber mounting on the replacement aluminium ones fitted snugly over the metal arms with no need to modify anything. There was just sufficient room for the new ones to fit without clashing together or bumping into things, but I did have to adjust all the key heights after fitting the pallets as the 4mm thick pads on the Hohner palettes were a bit different from the original thickness that varied from about 4.5 mm to a few that were only 1.5mm or so. Rather than do a bad job of bending key arms with pliers, I made some bending irons, that were similar to ones I saw online. I made mine from some half inch by one eighth brass strip that I obtained by the yard from a ship’s chandler. I knew that brass would be rigid enough, and it also had the merit of being easy for me to work and to soft solder. Whilst my brass bending irons were not the best looking ones out there, they did the job well, and there was something satisfying about making simple tools rather than buying them off the shelf.
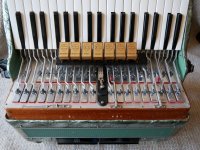
Once the keys, pallets, treble sliders and adjustments to the key height had been completed I proceeded to removing reeds from reed blocks, cleaning the reeds and the reed block, replacing the valves, and waxing the reeds back in place. I did one treble block at a time, generally each one took a day and a half to do. In the afternoon of the second day I would install the reed block back in the accordion and then I had the pleasure of hearing that part of the accordion’s voice for the first time.
The job of restoring the Scandalli was an adventure that took a few hours a day for 3 or 4 weeks. I had not done anything like this before, and was very new to playing accordions, having only begun that earlier in the year.
The little 12 bass Scandalli that I made my first accordion noises on, needed new valves, as evidenced by the clatter and flap of curled leather when ever low note were attempted, so my restoration of the 80 bass Scandalli really begun with opening up the 12 bass, taking out its reed blocks, removing the reeds, replacing the valves, and doing my first attempts at re-waxing.
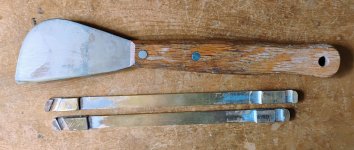
I made my own reed wax from 3 parts of beeswax, 1 part of pine resin and a few drops of linseed oil, and I made my own waxing tool after watching videos of Italian accordion makers waxing reeds with those half moon shaped tools that look rather like a modified cake slice. And yes I did go through the kitchen drawers to see if I could find something there that might work! In the end I flattened and reshaped an old paint scraper that was made out of heavy stainless steel, and had a simple wooden handle. Waxing reeds was terrifying at first, and my initial attempts were like the frenzied splashes of an abstract expressionist painter from the 1960s, but I learned a lot by being brave and giving it a try and I got better at it. I now enjoy the process and look forward to the delightful aroma of warm beeswax and pine resin that I heat up in an old electric crock pot.
With the 12 bass accordion back together again and working, it was time to have a serious look at the 80 bass Scandalli. When I acquired it, the instrument really was unplayable, with some notes not sounding in the treble, or groaning like an animal in pain. All the register switches were jammed, and when I popped the front cover off I could see that many of the pallets were in very poor condition owing to insect damage and, very strangely, what looked like an excess of heat that had distorted some of the pallets.
I realised that I would need to sort out the pallets before I could achieve a great deal, so I did a lot of searching online for replacements that would be suitable. Eventually I found that Wilson Music Services in Canada had a set of Hohner pallets that were in the“Discontinued and Hard to Find” section of their website, nice aluminium ones with red felt pads that were 49 x 13mm and just 1mm greater in length and width than the black plastic palettes on my Scandalli. I ordered them and hoped I could make them fit.

I removed all the treble keys, which was easy to do as each key was held in place by a small metal spring that could be unhooked from its attachment by using a little tool that Scandalli thoughtfully mounted in readiness just above the treble pallets. I attached a numbered sticky label to each of the keys and laid them out in order as I removed them so that I would have less difficulty sorting out the puzzle when I put them back together again. I gave all of the keys a good clean, and also got into all the nooks and crannies behind them with the vacuum cleaner and got rid of 60 years worth of dust! On close inspection of the keys I found some of them had fine metal fragments imbedded in them. I wondered if the instrument had been left open on a bench in a workshop near where someone was grinding metal or welding?
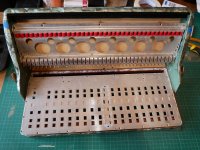
With treble keys removed, I took the opportunity to investigate the treble register selectors. It transpired that these were not working because the register slides had all jammed due to corroding and forming almost commercially exploitable quantities of aluminium oxide! The slides occupy a space between two sheets of metal like bacon sandwiched in between two slices of bread. Annoyingly I could find no way of separating the metal plates, but eventually got the register slides moving by inserting a small screwdriver into the narrow gap between the plates and gently levering away at this until I could get the slides to budge a tiny bit at a time. I hated having to use a screw driver in this manner, but it worked and eventually I was able to remove the slides and carefully clean them, before putting them in their slots again. It was a considerable relief to get them going again.
I removed the old pallets by carefully heating the metal arm that they were attached to with a soldering iron. All of them dropped off easily, and I was delighted to find that the rubber mounting on the replacement aluminium ones fitted snugly over the metal arms with no need to modify anything. There was just sufficient room for the new ones to fit without clashing together or bumping into things, but I did have to adjust all the key heights after fitting the pallets as the 4mm thick pads on the Hohner palettes were a bit different from the original thickness that varied from about 4.5 mm to a few that were only 1.5mm or so. Rather than do a bad job of bending key arms with pliers, I made some bending irons, that were similar to ones I saw online. I made mine from some half inch by one eighth brass strip that I obtained by the yard from a ship’s chandler. I knew that brass would be rigid enough, and it also had the merit of being easy for me to work and to soft solder. Whilst my brass bending irons were not the best looking ones out there, they did the job well, and there was something satisfying about making simple tools rather than buying them off the shelf.
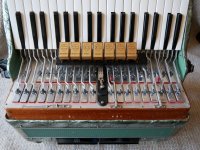
Once the keys, pallets, treble sliders and adjustments to the key height had been completed I proceeded to removing reeds from reed blocks, cleaning the reeds and the reed block, replacing the valves, and waxing the reeds back in place. I did one treble block at a time, generally each one took a day and a half to do. In the afternoon of the second day I would install the reed block back in the accordion and then I had the pleasure of hearing that part of the accordion’s voice for the first time.