Jose EB5AGV
Always learning!
Well, I have explained in another thread that I have got a second HOHNER VERDI II. Yes, I am that way, when something fails I try to get a way to deal with it. So, when my first VERDI II revealed its dark inner secret (rusted reeds), I began to think what I could do, as that instrument has an history behind which urged me to fix it. So I checked the usual second hand sites, looking for a parts donor, but instead found this one:
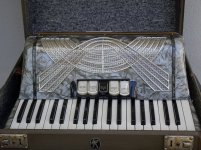


So, even if knowing that it would not be what I initially intended, it looked like a good accordion and, well, I was eager to finally play a VERDI II. And, this time, the seller assured me everything worked and explained it was his instrument, same model he played back in the days, bought used about 8 years ago, and now he was unable to play it due to an injury. So, well, I went for it.
But on arrival, there was some damage on one key

Luckily the break was clean and the broken part was there. So, well, I tried to play the instrument... and the bass mechanism was sluggish and lots of bass notes played without pressing anything. So it was impossible to check it that way. Oh well...
I first looked at the treble mechanism and found that everything is nice and the felts look pretty well:
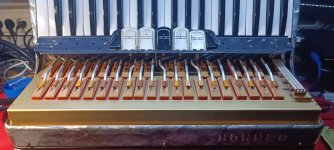

So it was time to reveal if the instrument was worth it or not... I had my recent experience with the other unit, so I knew how to get into the instrument to check everything. I used this foam part to set the pins in order:
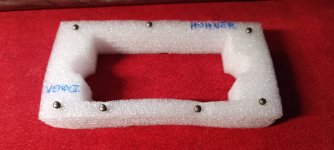

BTW, the pins were easy to take out, which was quite a lot different than on the other one, which had some rust on the pins. These were mostly clean. So, how would the reeds be???. Maybe I had another door stopper???. No, they are in great shape!!!
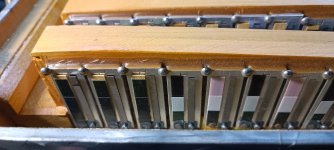
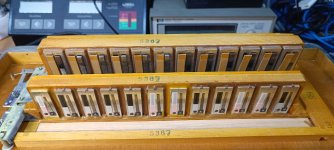
Even the valves are mostly fine, except for some bass ones.
(continues on next message)
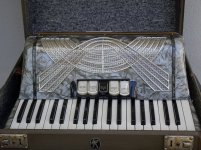


So, even if knowing that it would not be what I initially intended, it looked like a good accordion and, well, I was eager to finally play a VERDI II. And, this time, the seller assured me everything worked and explained it was his instrument, same model he played back in the days, bought used about 8 years ago, and now he was unable to play it due to an injury. So, well, I went for it.
But on arrival, there was some damage on one key


Luckily the break was clean and the broken part was there. So, well, I tried to play the instrument... and the bass mechanism was sluggish and lots of bass notes played without pressing anything. So it was impossible to check it that way. Oh well...
I first looked at the treble mechanism and found that everything is nice and the felts look pretty well:
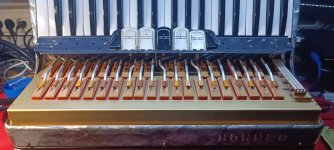

So it was time to reveal if the instrument was worth it or not... I had my recent experience with the other unit, so I knew how to get into the instrument to check everything. I used this foam part to set the pins in order:
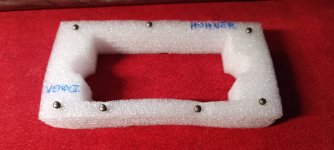

BTW, the pins were easy to take out, which was quite a lot different than on the other one, which had some rust on the pins. These were mostly clean. So, how would the reeds be???. Maybe I had another door stopper???. No, they are in great shape!!!

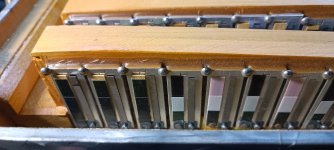
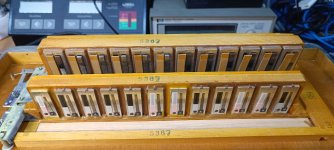
Even the valves are mostly fine, except for some bass ones.
(continues on next message)